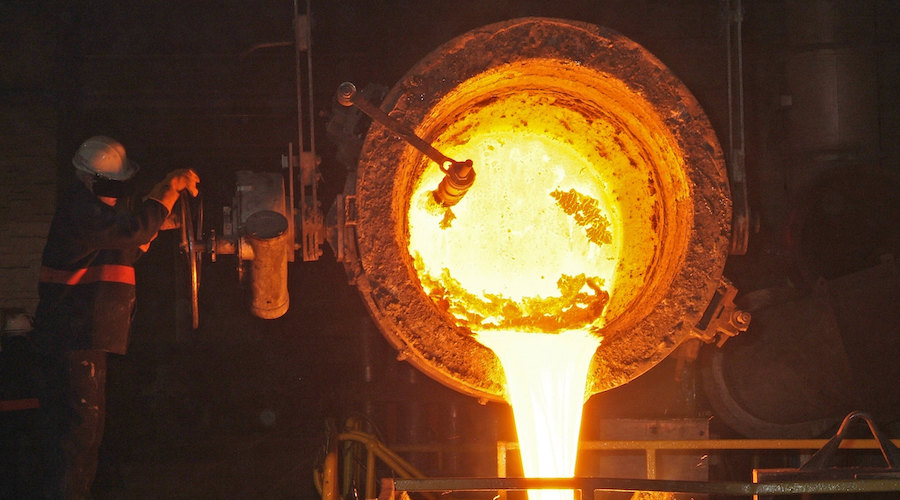
The study shows that as an aluminum-copper alloy cools the solidification process starts with the formation of faceted dendrites, which are formed by a layer-by-layer stacking of basic units that are just micrometres in size. These units start out as L-shaped and stack on top of each other like building blocks, but as they cool they change shape and transform into a U shape and finally a hollowed-out cube, while some of them stack together to form beautiful dendrites.
“The findings from this new study provide a real insight into what happens at a micro level when an alloy cools, and show the shape of the basic building blocks of crystals in molten alloys,” lead author Biao Cai said in a media statement. “Crystal shape determines the strength of the final alloy, and if we can make alloys with finer crystals, we can make stronger alloys.”
According to Cai, the results are in direct contrast with the classical view of dendrite formation in cooling alloys and open the door to developing new approaches that can predict and control the formation of intermetallic crystals.
Previous research by Cai and his team has already resulted in a novel technology to improve the quality of recycled aluminum by removing iron from the molten alloy in a simple, inexpensive process that uses magnets and a temperature gradient.
The technology is the subject of a patent application filed by the University of Birmingham Enterprise and it has also attracted funding from the Midlands Innovation Commercialization of Research Accelerator and the EPSRC-Impact Acceleration Account.
The funding has enabled Biao to build a large-scale prototype that runs to 1000 C and uses a 1 Tesla magnet, which is currently being tested using ingots provided by the Tandom Metallurgical Group, a producer of aluminum alloys, master alloys and recycled aluminum products, scraps and drosses.