Teck’s technology transformation initiatives enhance performance, safety and sustainability
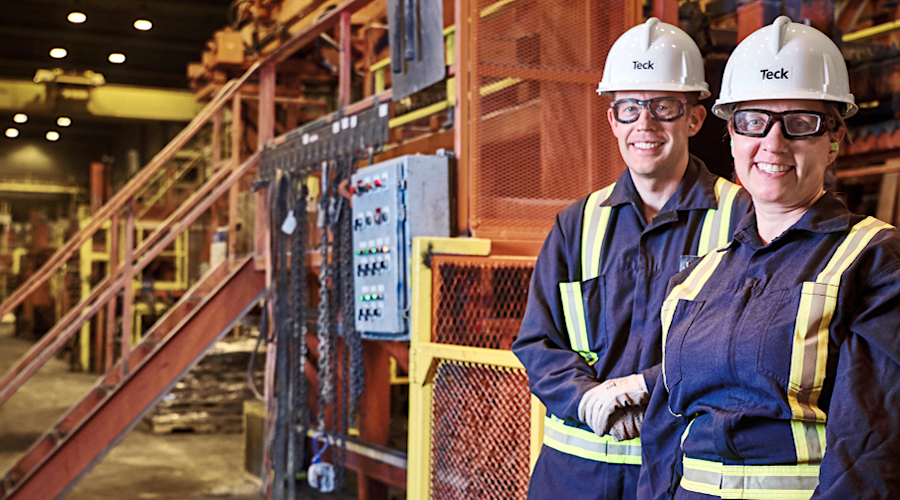
Teck said RACE, which stands for Renew, Automate, Connect and Empower, between 2019-2021 enhanced operational performance in these core areas:
Mine Optimization – Leveraging data, machine learning and digital applications across Teck’s mining equipment has increased truck productivity by up to 10% at certain operations, reduced drilling and fuel costs, and optimized the quality of material going to processing plants. At British Columbia’s Fording River Operations, machine learning models use real-time information such as truck speed and location to quickly identify road maintenance tasks and the optimal allocation of trucks to maximize production.
At Red Dog Operations in Alaska, visualization and 3D modelling applications are used to accurately predict the movement of material during a blast, improving the zinc grade delivered to the plant by about 5%. Similar approaches at Elkview Operations in BC reduced ash variability of material in the plant, increasing plant yield by approximately 0.5% starting in December 2021.
Processing Improvements – Automation and machine learning models within Teck’s processing plants increased throughput capacity by up to 9%, and recovery by up to 3% at certain sites. At Red Dog Operations, automation has been used to improve stability of grinding mill processes, increasing production rates by 9%, Teck said.
At Highland Valley Copper Operations in British Columbia, automation and machine learning models that use real-time information from flotation processes – such as chemical addition and equipment settings – resulted in a 3% increase in copper recovery. Combined with simulation models that track ore characteristics through our grinding mills, process control enhancements and data analytics that support more informed blasting decisions, the site has realized a 15% increase in mill throughput capacity.
Integrated Operations and Maintenance – Digital planning applications that better connect operations with logistics teams have reduced costs and maximized throughput between Teck’s steelmaking coal operations and the recently upgraded Neptune Bulk Terminals. Automated train loading at Fording River Operations has increased loading per car by 2% and loading speed by 40%. Predictive maintenance enabled by equipment sensors has reduced equipment downtime and operational interruptions across all sites.
Reducing Health & Safety Risk: Safety initiatives at various Teck operations, including light vehicle monitoring systems, collision and proximity detection and autonomous haulage systems, have reduced the overall risk associated with vehicle interactions and contributed to a 38% reduction in Teck’s high-potential incident frequency in 2021 compared to the previous year.
Enhancing Sustainability: The company said digital technology is being implemented across Teck operations to improve decision making in the areas of water use, air quality and energy consumption.
At Trail Operations in BC various automation initiatives increased throughput of the KIVCET dryer and at the same time reduced sulphur dioxide emissions by 19% in 2021 compared to the previous year. At Fording River Operations, Teck is developing machine learning using weather and water quality data to provide enhanced operational recommendations for water storage and movement within the mine.
These RACE21 initiatives follow Teck’s other technology programs, including adoption of saturated rock fill technology for Elk Valley Water Quality Program, which has accelerated the implementation of water treatment in the Elk Valley in British Columbia and offers a sustainable long term alternative to conventional tank-based treatment plants.